Our specialist will help you choose the most suitable configuration for you. We can arrange everything over the phone, by e-mail or at a meeting. The LEGIPOL team is at your disposal.
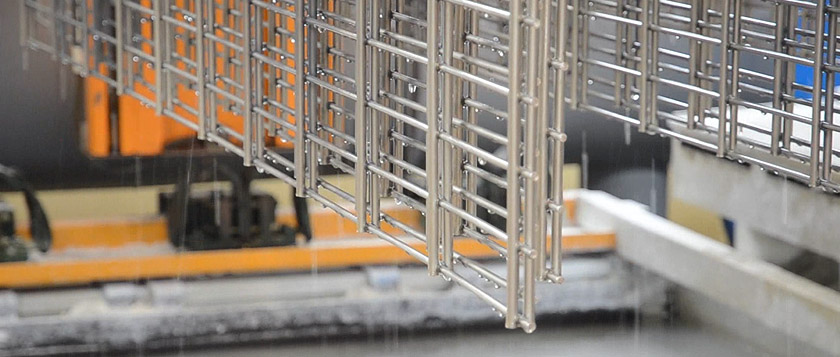
ELECTROGALVANISING
LEGIPOL has been on the market since 1995. We have our own hot-dip galvanising and electrogalvanising facilities as well as a powder coating plant.
In order to meet the expectations of our customers, we offer comprehensive services starting with the preparation of the surface of a component
through the process of electrogalvanising or hot-dip galvanising and subsequent powder coating in a colour chosen by the customer.
Electrogalvanising was introduced in our company in 2008.
We specialise in the application of alkaline zinc to steel products.
We use environmentally friendly substances in this process and the resulting coating is homogeneous and shiny.
The coating is finished with a bluish passivation layer, which additionally protects the details against corrosion.
On request, we can provide a matt, colourless coating and protect the parts with a yellowish passivation.
The tanks in our galvanising facility can accommodate workpieces with maximum dimensions of 170 mm x 2500 mm x 3000 mm (depth x height x width), and the maximum weight of a single workpiece is 150 kg.
We have the option of varying the thickness of the zinc coating from 8 to 12 um, depending on the customer's requirements.
The resulting layer protects the workpiece from corrosion and is ideal for further processing - powder coating, which we also offer.
HOT-DIP GALVANISING
This method offers very durable, weatherproof protection. The workpiece is immersed in a bath filled with molten zinc at a temperature of 450 °C. The metals melt at the interface between the steel and zinc, forming a resistant anti-corrosion layer. In addition, the decomposition products of the zinc form a poorly soluble and chemically resistant layer on the surface on contact with the air, which passivates the fence surface and slows down its oxidation process.
Advantages
ELECTROGALVANISING
Galvanisation is carried out using an electrolysis process. The surface of the fence is degreased and immersed in an electrolytic bath, allowing the steel mould to be coated with a precise and smooth layer of zinc. A chromium passivation layer is also applied to the galvanised mesh panels to provide the zinc with additional protection against oxidation.
Advantages
POWDER COATING
Thanks to electrostatics, the component to be painted is coated with a powder in the selected colour and heated to a high temperature at which the powder melts and polymerises. Unlike wet painting, powder coating does not release any harmful solvents into the atmosphere. Importantly, the powder that has not settled on the material can be reused in the next cycle. The coating is resistant to corrosion, chemicals, heat and mechanical damage.